铝型材冲孔模具结构设计(含CAD图)
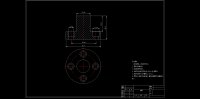
铝型材冲孔模具结构设计(含CAD图)(任务书,开题报告,论文说明书13000字,CAD图6张合一)
摘 要
这篇文章按照冲孔模具设计的原理与能够查阅到的基本方法,通过研究铝合金,根据铝型材设计的相关经验公式确定模具结构具体参数,三维建模导入有限元软件进行应力分析。需要该模具应力分布相对均匀。通过上述得出的结果,提出较为完善的模具设计方案。并详细的介绍了我在设计铝型材冲孔模具过程中,通过公式所得出的具体数据,反复检验后计算得到的较为适合的结构,以及有限软件进行分析时的大致过程等。使用软件分别是:模具的具体三维模型通过FREECAD建立,应力分析通过ANASYS软件进行,并进行结构优化,最终得到应力分布图。
关键词:冲孔模具;铝型材;结构设计;应力分析与校核
Abstract
In this paper, according to the principle of punching die design and the basic method available, the specific parameters of die structure were determined according to the relevant empirical formula of aluminum profile design through the study of aluminum alloy, and the 3d modeling was imported into the finite element software for stress analysis. The die stress distribution should be relatively uniform. Through the above results, the more perfect mold design scheme is proposed. In addition, it introduces in detail the specific data obtained through the formula in the process of designing the punching mold for aluminum profiles, the relatively suitable structure obtained after repeated inspection, and the general process in the analysis with the limited software. The software used is: the specific 3d model of the mold is established through FREECAD;Stress analysis was carried out through anasy software, and the structure was optimized, and the stress distribution diagram was finally obtained.
Key words: Punching die;Aluminum;Structural design stress;Analysis and check
[资料来源:Doc163.com]
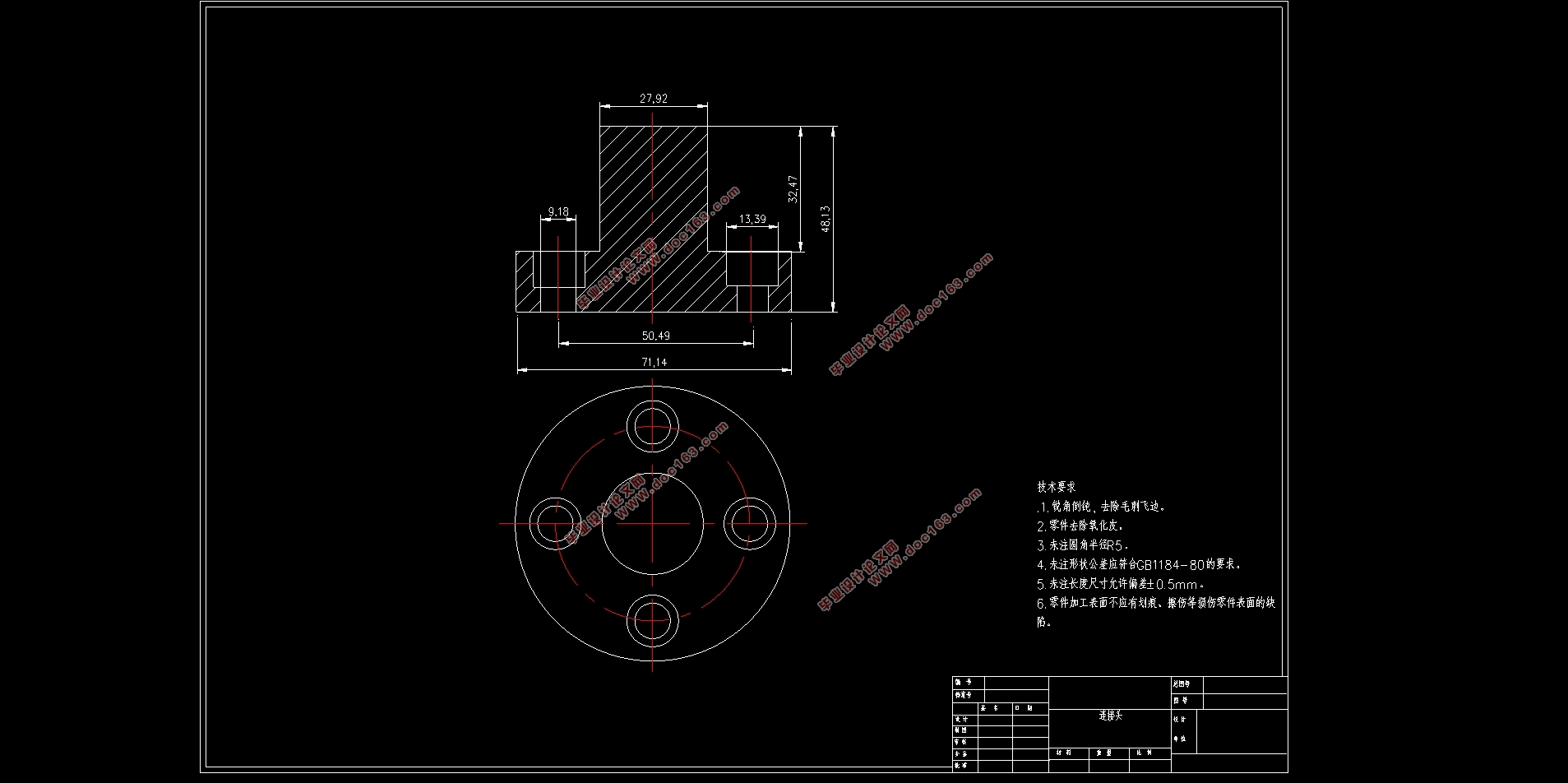
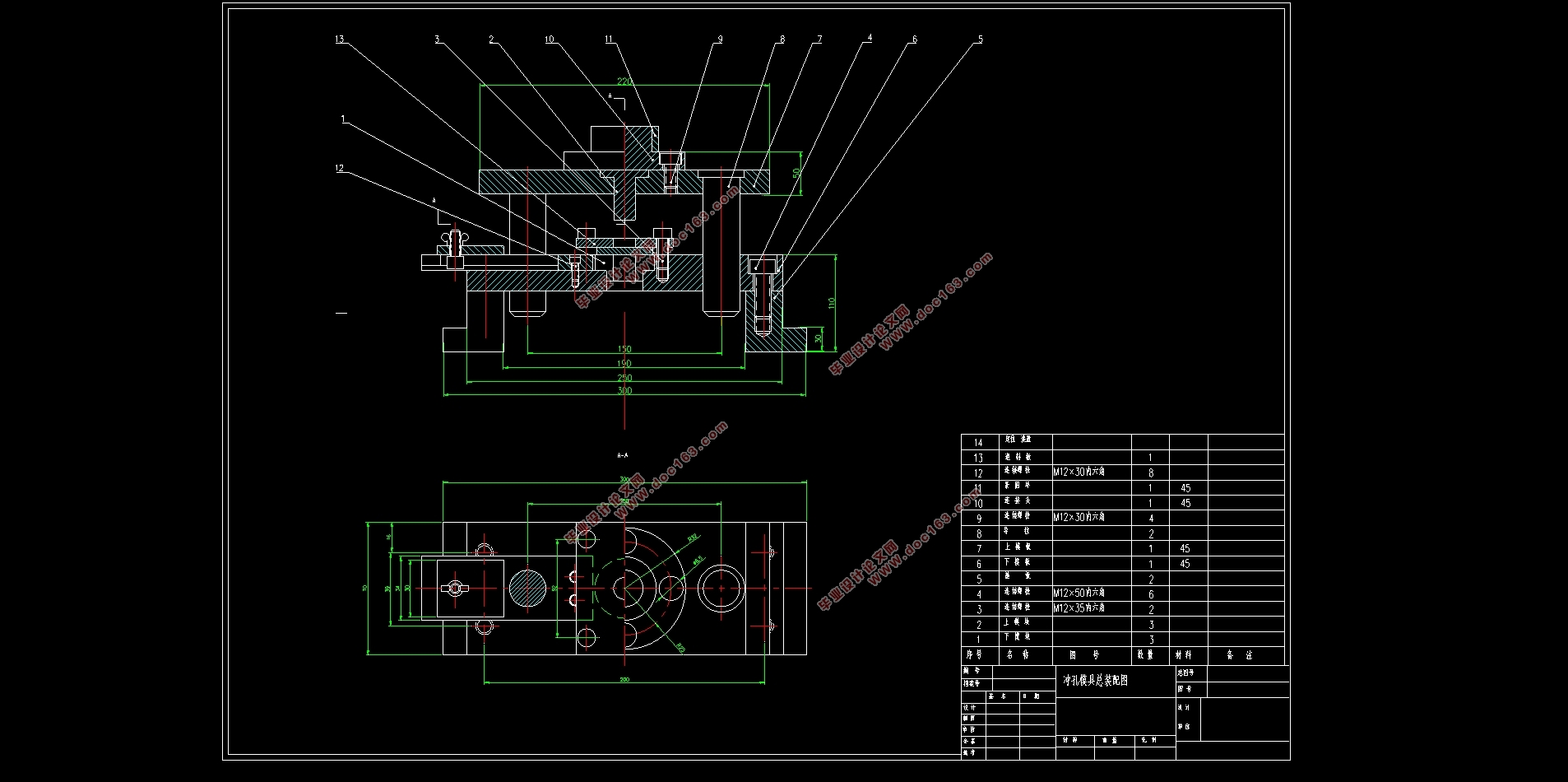
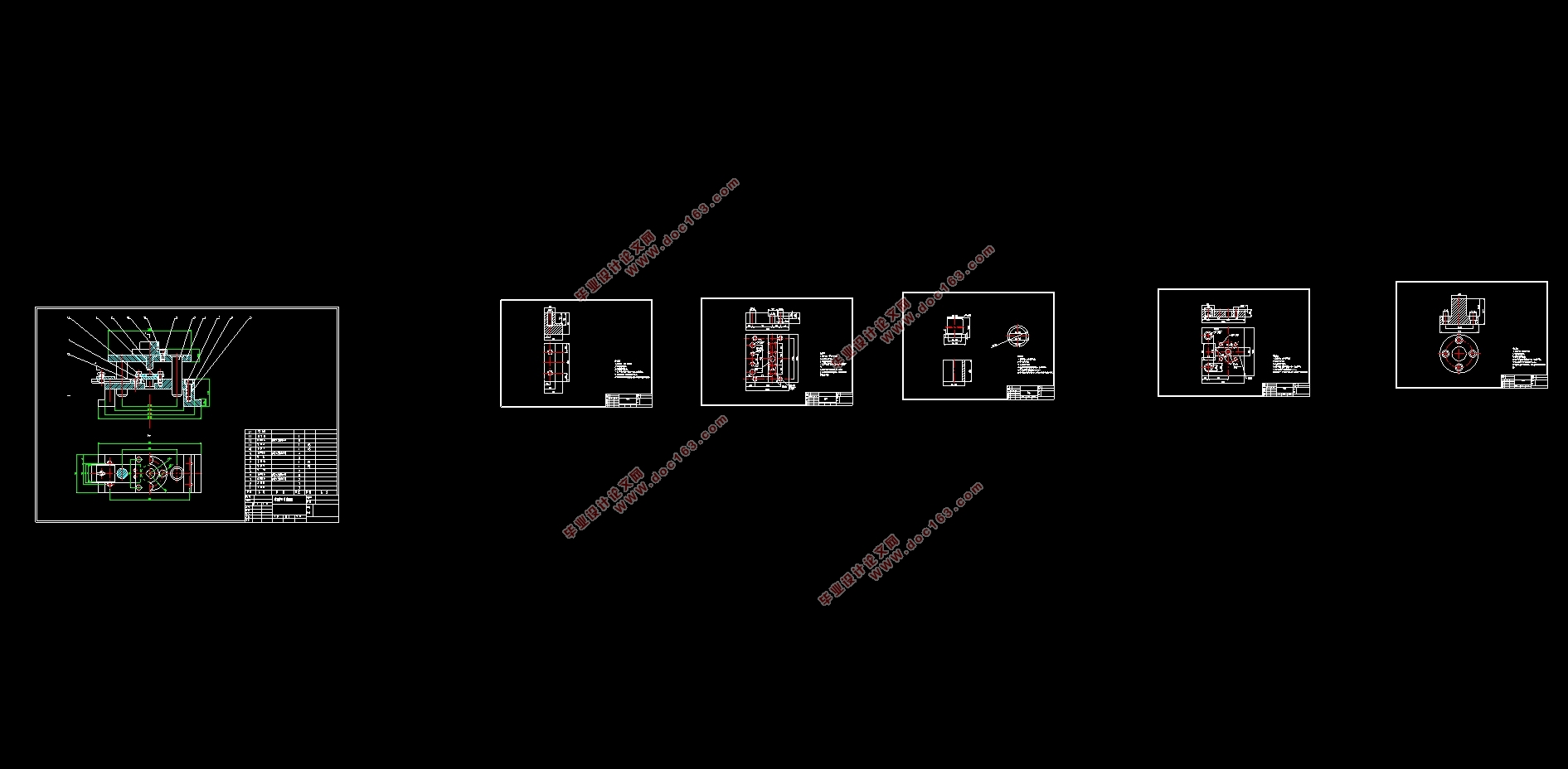
目录
第1章 绪论 1
第2章 铝合金门窗的材料 2
2.1 选取铝合金门窗的材料 2
2.2铝型材的工艺流程 3
2.3铝合金型材主要工艺流程 3
2.4冲孔件的偏差和限制 5
2.5冲孔件的尺寸分析 5 [资料来源:http://Doc163.com]
第3章 模具结构设计 7
3.1模孔的配置 7
3.1.1单孔模孔的配置 7
3.1.2多孔模孔的配置 8
3.2 模具的工作条件及其结构分析 9
3.2.1工作条件 9
3.2.2结构分析 9
3.3 制定冲孔件截面图 10
3.4 冲孔方式的确定 10
3.5 冲孔件的毛边形式的尺寸 11
3.6 选择冲孔压力机 12
3.7 冲孔模上模具刀口厚度 12
3.8 模具材料 13
3.9合理使用模具 14
3.9.1如何调整冲孔模具 14
3.9.2在使用时应注意的问题 14
第4章 构造模具三维模型和应力分析 16
4.1实验材料 16
4.1.1实验设备及相关软件 16
4.1.2 FREECAD的介绍 16
4.1.3 ANSYS的介绍 16
4.2设计过程 16
[来源:http://www.doc163.com]
4.2.1利用FREECAD设计出模具结构 16
4.2.2利用ANSYS分析装配件应力 21
第5章 总结和展望 24
5.1 建模与有限元分析总结 24
5.2 模具未来发展展望 24
参考文献 26
致 谢 27